LASER CLADDING
Our process involves the use of a high-energy laser to melt and fuse a powdered or wire feedstock material onto the surface of the component - forming a metallurgical bond.
The cladding head is mounted to a robot or CNC machine programmed to accurately follow the surface of the component being cladded.
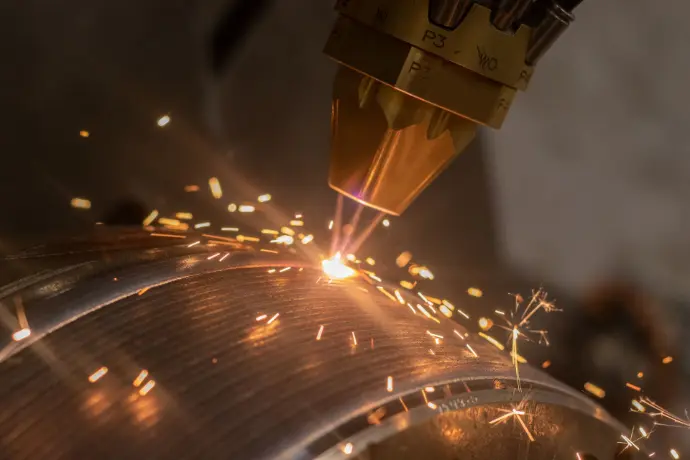
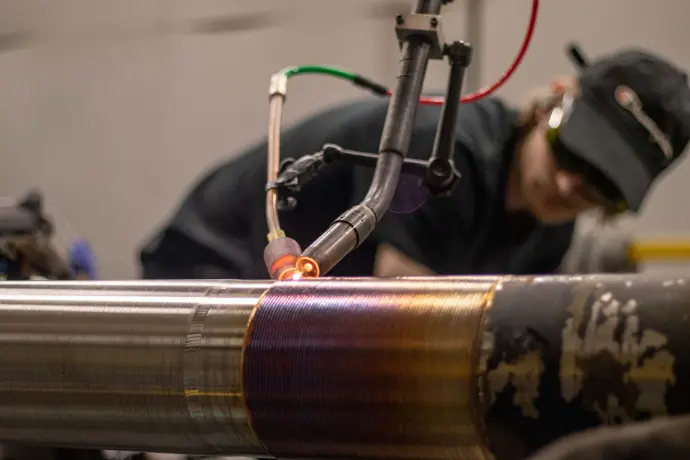
Benefits of Laser Cladding
Rapid turn around
Superior wear protection
Superior corrosion protection
Metallurgical bond
Minimal part distortion
Higher productivity
Reduced downtime
Applications
Thread/spindle repair
Oil & Gas downhole tooling
Motor shaft repair and refurbishment
Mining, drilling and blasting tool repair
Wind turbine shaft refurbishment
Plastic injection, compression tool repair and refurbishment
Pump components
Impellers
Housings
Wear Rings
Valve components
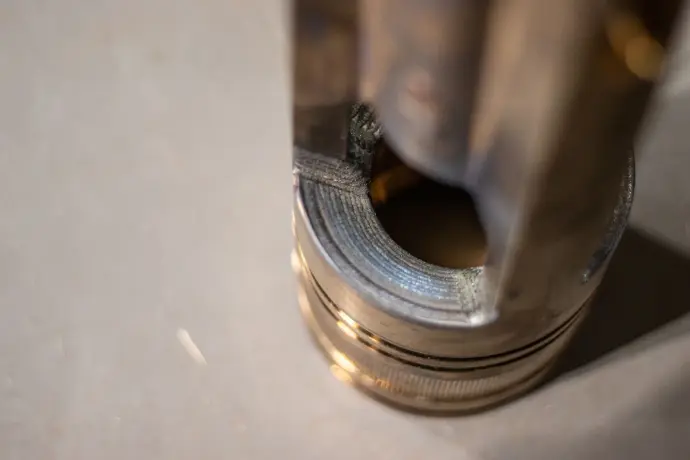
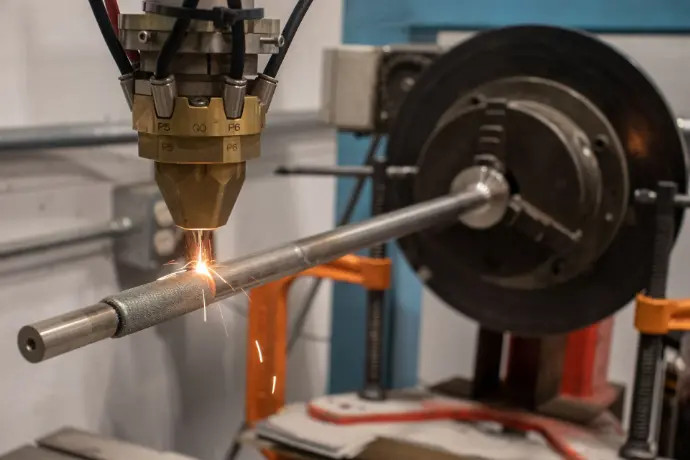
Advantages
Minimal dilution is achieved to keep the desired properties of the cladding material
Low heat input - ideal for finished and near-finished components
Large powder metal alloy inventory and custom alloy blends
Variable beam size allows for cladding parts of different size/thickness (laser hard-facing as little as 0.010" and as much as 0.060" per pass)
Coating thickness can be applied to near net shape to minimize post process machining
Well suited for robot control, giving excellent process replication
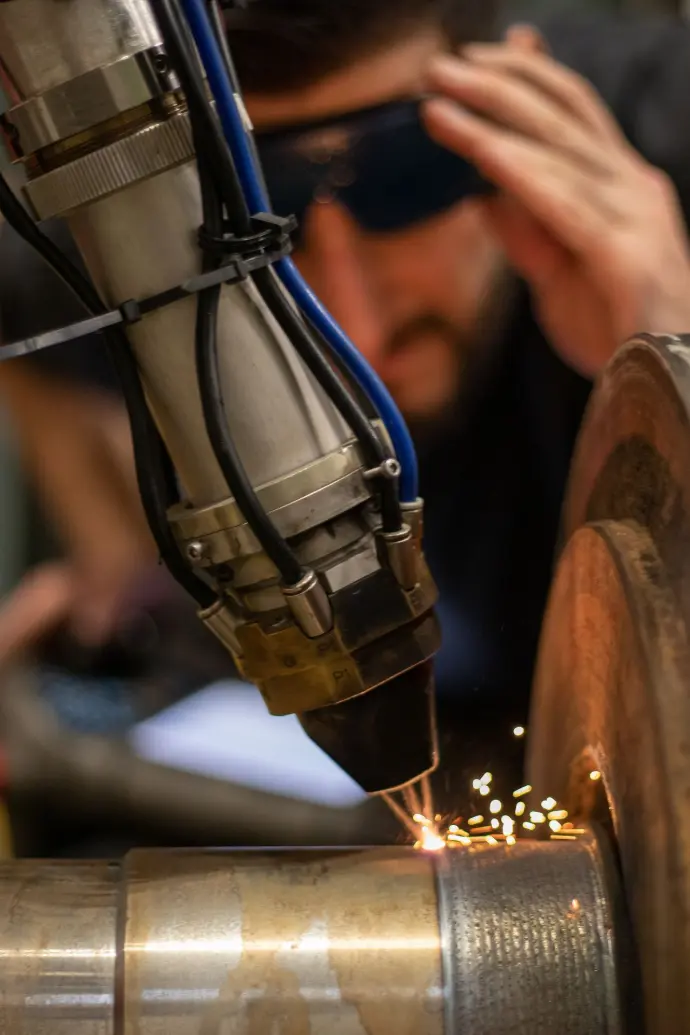
Capabilities
8KW diode laser
2 6KW diode lasers
4KW fiber laser
2KW fiber laser
8 6-axis robots
Large work envelopes (30'x12'x12')
Coaxial and off-axis cladding heads
ID cladding head capable of cladding IDs as small as 3.25"
Variable spot sizes allow for tailoring to individual jobs
Full 3D modeling and CAM control ensures repeatability and accuracy
Off-line simulation for quick and accurate development
Metallic powder, cold wire and hot wire cladding
Controlled heat input through real-time measurement of melt pool
Large cladding lathe with 100,000lbs capacity - 72" swing and 220" length